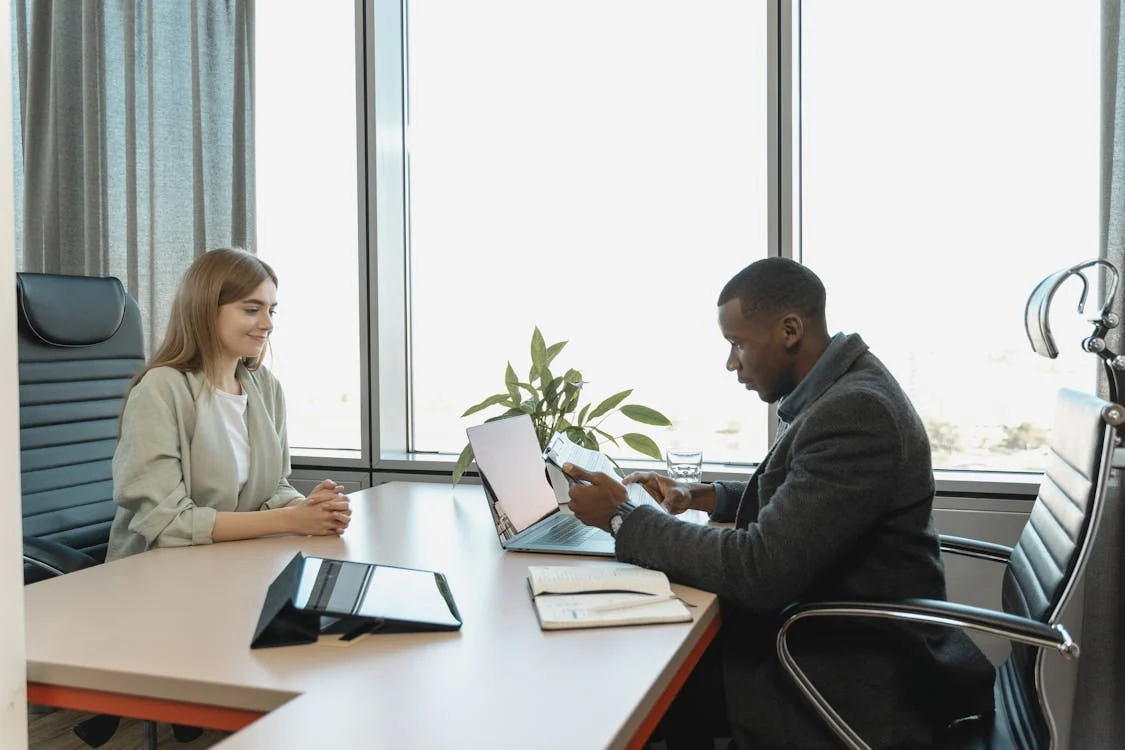
Understanding the Plant Manager Role
A plant manager plays a crucial role in overseeing a facility's daily operations. This involves coordinating various activities to ensure smooth production processes. They are responsible for implementing lean manufacturing principles, which help to eliminate waste and improve efficiency within the plant.
Leadership is a key aspect of the plant manager's responsibilities. They must guide teams, set clear expectations, and foster a productive work environment. Effective leadership means listening to staff and encouraging open communication to address issues promptly.
Quality control is another important duty. Plant managers enforce strict standards to guarantee that the products meet industry requirements. Adherence to safety protocols is essential to protect workers and compliance with regulations.
Strategic planning is vital for long-term success. Plant managers use strategic planning skills to anticipate challenges and adapt to market changes. They also need technical knowledge to understand the machinery and processes used in production.
Budget management is part of the plant manager's role as well. Monitoring expenses ensures that the plant operates within budget while achieving desired plant performance. This involves analyzing costs and finding ways to optimize resource use.
Each manager has their own management style. Effective managers often blend strong decision-making abilities with a collaborative approach. This balance helps maintain harmony among staff while pushing for efficiency and performance improvements.
Essential Leadership Competencies
Understanding key leadership competencies helps plant managers effectively guide their teams and maintain productivity. These competencies include evaluating leadership skills, communication, decision-making and strategic planning, and building teamwork.
Evaluating Leadership Skills
Leadership skills are crucial for plant managers to inspire and guide teams. Evaluating these skills involves observing a leader's ability to motivate and foster a positive working environment. It's important to recognize how managers set a vision for their team and lead by example, ensuring alignment with the company's goals. Developing adaptability and resilience is essential, as managing unexpected changes effectively can significantly impact morale and productivity. Plant managers who possess strong leadership skills can drive transformation and growth.
Influence and Communication Skills
Effective communication is a core competency for plant managers. Clear and concise communication ensures team members understand objectives and roles, reducing errors and misunderstandings. Managers should practice active listening to genuinely connect with team members, gaining trust and fostering open dialogue. Nonverbal cues, such as body language and tone of voice, play crucial roles in conveying messages. A plant manager's influence often hinges on strong communication skills, which help in persuading stakeholders and facilitating collaborations.
Decision-Making and Strategic Planning
Decision-making and strategic planning are pivotal for plant managers to navigate complex challenges. It involves analyzing data and weighing potential outcomes before implementing decisions. Managers should establish a structured approach to strategic planning, setting clear goals and developing actionable steps to achieve them. This requires foresight and flexibility, as plans may need adjustments based on evolving circumstances. Effective decision-making processes contribute to sustained operational success and better risk management.
Building and Leading Teamwork
Building teamwork involves creating an environment where team members collaborate effectively. Plant managers should encourage diverse groups to work together by fostering inclusiveness and mutual respect. Leadership style greatly influences team dynamics; adopting a collaborative approach often leads to higher engagement and creativity. Managers can also organize team-building activities to strengthen relationships and ensure members feel valued. A focus on teamwork leads to improved problem-solving and innovation.
Proficiency in Production and Operations
Proficiency in production and operations is essential for effective plant management. Key areas of focus include managing processes, achieving goals, and implementing lean principles while ensuring quality and safety standards are upheld.
Managing Production Processes
Effective management of production processes is crucial for plant managers. This involves planning, organizing, and overseeing the production schedule to ensure smooth operations. A plant manager needs to track performance metrics and analyze data to identify areas for improvement.
Tools like Gantt charts and ERP systems can help in coordinating tasks and resources. Communication plays a vital role, as does the ability to adapt to changes quickly. Managers must ensure machinery is well-maintained and downtime is minimized to keep the production line running efficiently.
Achieving Production Goals
Achieving production goals requires setting clear objectives aligned with company strategies. Plant managers must balance resource availability with production demands. They often employ capacity planning and demand forecasting to anticipate needs.
Managers strive to optimize the use of labor, materials, and time to meet targets. Strategies may include adjusting shifts or re-allocating resources based on priority. Regular reviews and adjustments help ensure targets are met while maintaining cost-effectiveness.
Implementing Lean Principles
Lean principles focus on minimizing waste and maximizing productivity. Plant managers use these principles to streamline operations, often through continuous improvement practices like Kaizen. Implementing techniques such as just-in-time (JIT) inventory and value stream mapping can reduce excess.
Managers encourage team involvement in identifying inefficiencies. The goal is to create a culture where every employee looks for ways to improve processes. Measuring the impact of these changes is important to demonstrate their effectiveness and foster ongoing improvements.
Quality Assurance and Control
Quality assurance and control are pivotal in maintaining product standards. Plant managers must establish and monitor quality standards throughout the production process. This includes setting quality control checkpoints and using standardized testing procedures to maintain consistency.
Training staff on quality protocols and conducting regular audits ensures compliance. Integrating technology such as automated quality inspections can enhance consistency. Managers address any deviations immediately to maintain product integrity and customer satisfaction.
Maintaining Safety Standards
Maintaining safety standards is non-negotiable in production environments. Plant managers ensure compliance with safety regulations to protect workers and assets. Implementing regular safety training and drills keeps staff prepared for potential hazards.
A proactive approach involves risk assessments and safety audits to identify potential issues before they arise. Effective communication of safety protocols and having a feedback loop where employees can report concerns is vital. Ensuring the workplace is secure fosters a productive and safe working environment.
Demonstrating Technical and Problem-Solving Abilities
Technical skills and the ability to solve problems are key traits for plant managers. They ensure efficient operations and continuous improvement in production processes, leading to better performance and results.
Applying Technical Expertise
Plant managers must use their deep technical expertise to oversee production processes. This involves understanding machinery, production lines, and equipment operations. They analyze technical performance and identify areas for improvement.
Regular inspections and routine maintenance are vital. Technical expertise also helps them troubleshoot equipment failures. Plant managers provide guidance and training for the team on technical matters. They use these skills to ensure safety standards and minimize downtime in the plant.
Innovating with Continuous Improvement
Continuous improvement is essential to plant success. Managers implement strategies to enhance productivity and efficiency. They need to identify weak points in processes using data analysis.
Implementing Lean Manufacturing and Six Sigma techniques can help. These approaches focus on reducing waste and optimizing workflows. Managers encourage feedback from employees and conduct regular reviews. By fostering innovation, they drive the plant toward operational excellence.
Addressing Complex Challenges
Complex challenges require strong problem-solving skills. Managers are adept at identifying issues that may disrupt workflow, such as supply chain disruptions or equipment failures.
They use a structured approach to problem-solving: first identifying the root cause, then developing viable solutions. Collaboration with the team is essential, ensuring all perspectives are considered. Problem-solving abilities also include managing emergencies efficiently, prioritizing tasks, and taking decisive actions to restore normal operations.
Optimizing Operations and Resources
Effective management of plant operations involves fine-tuning various processes to ensure efficiency and resourcefulness. Key areas include adjusting production schedules, allocating resources wisely, and minimizing waste through solid inventory control.
Streamlining Production Schedules
Efficient production scheduling is vital for maximizing output and meeting demand. Plant managers should utilize lean manufacturing principles to eliminate delays. Implementing advanced planning systems aids in accurately forecasting demand. These systems help in aligning workforce availability and machine capabilities with production needs. Regular assessments and adjustments allow the production schedules to remain flexible. This enhances adaptability to any sudden changes in order priority.
Understanding bottlenecks and addressing them promptly ensures continuous flow on the production line. Emphasizing teamwork and clear communication among departments minimizes disruptions. Coordinating with suppliers for timely delivery of materials further supports a seamless operation, reducing downtime and improving productivity.
Effective Resource Allocation
Making good use of resources is crucial for cost-effective operations. Managers must identify and allocate resources based on skills, equipment capabilities, and production demands. Prioritizing tasks according to their impact on overall plant efficiency is essential. A thorough analysis of resource usage helps in decreasing downtime and increasing employee productivity.
Implementing a cross-training program enhances workforce versatility, allowing employees to shift between roles as required. This flexibility minimizes disruptions during unexpected absences. Managers should also monitor utilization rates of machinery to avoid overuse. Timely preventive maintenance schedules can maximize lifespan and improve reliability, ensuring smooth operation.
Inventory Management and Waste Reduction
Proper inventory management is vital for reducing waste and managing costs. Lean manufacturing principles call for a just-in-time (JIT) approach, minimizing excess stock while meeting production needs. Regular audits help track inventory levels and prevent overstocking or shortages, which can disrupt production.
Reducing waste involves identifying inefficiencies in materials handling and usage. Implementing recycling programs and reusing materials where possible cuts down waste. Encouraging employee involvement in waste reduction strategies fosters a culture of accountability and responsibility. Reviewing waste outputs regularly and adjusting processes enhances sustainability and reduces environmental impact. Start with small changes and build momentum towards significant waste reduction successes.
Human Resources and Team Development
Effective management in plant operations includes focusing on human resources and team development. Key areas include conducting performance evaluations to assess and improve employee performance, fostering employee training to maintain a skilled workforce, and promoting cross-functional collaboration to enhance teamwork across departments. Each serves as a crucial element in nurturing a productive and harmonious work environment.
Conducting Performance Evaluations
Performance evaluations are vital for monitoring and improving employee performance. During evaluations, managers can identify strengths and areas for improvement. It's important to give clear, actionable feedback. Managers should use objective criteria, such as attendance records and project outcomes, to ensure fairness. Regular evaluations can boost morale and keep employees motivated.
Involving human resources helps streamline the evaluation process. They offer guidelines and tools to keep assessments consistent. Collaboration between HR and plant managers ensures evaluations truly reflect employees’ contributions.
Fostering Employee Training
Training programs are essential for skill enhancement and career growth. Offering regular training keeps employees updated with the latest technologies and processes. This can lead to improved efficiency in daily operations. Managers should work with HR to identify training needs and select suitable programs. Employees should have access to both in-house and external learning opportunities.
Targeted training not only boosts individual skills but also closes knowledge gaps within teams. By emphasizing training, companies invest in their workforce, leading to better retention rates and job satisfaction.
Promoting Cross-Functional Collaboration
Encouraging cross-functional collaboration improves team dynamics and project success rates. When employees from different departments work together, they bring diverse skills and perspectives. This can lead to innovative solutions and faster problem-solving. Managers should facilitate regular interaction among departments through meetings or team-building activities.
Human resources can assist by organizing workshops that focus on collaboration and communication skills. By fostering these interactions, plants can create a more cohesive and efficient team environment, ultimately benefiting the entire organization.
Focusing on Business Acumen and Project Management
Ensuring efficiency in plant operations requires strong business acumen and project management skills. Plant managers must handle budgets carefully and meet project deadlines effectively.
Overseeing Budgets and Financials
Budget management is crucial for plant managers. They need to keep track of expenses and revenues. It involves creating a budget, adjusting it as needed, and ensuring funds are used efficiently. Monitoring financial KPIs can help make informed decisions. These might include cost per unit, return on investment, and operating expenses.
Effective budget oversight helps prevent overspending and leads to smarter resource allocation. A plant manager's ability to manage budgets well ensures financial stability and operational success.
Managing Projects and Deadlines
Project management is key for plant managers. Handling multiple projects requires careful planning and resource allocation. Managers need to set clear goals and use project management tools to track progress and deadlines. Meeting deadlines helps maintain productivity and avoid disruptions.
Using productivity KPIs such as throughput and quality rates can help optimize processes. Managers benefit from creating detailed timelines and assigning tasks based on team strengths. This organized approach supports a smooth workflow and timely project completion.
Enhancing Relationships and Networking
Building strong industry connections is essential for plant managers. Focusing on managing supplier relationships and engaging with cross-industry partners can lead to improved operations and increased customer satisfaction.
Managing Supplier Relationships
Plant managers play a critical role in maintaining strong supplier relationships. Clear communication and understanding of industry standards are crucial. By setting expectations and providing feedback regularly, managers ensure that suppliers meet quality and timing requirements. This collaboration helps reduce disruptions in the manufacturing environment and enhances product quality.
Effective negotiation skills also contribute to cost management. Developing mutual trust with suppliers encourages them to prioritize the plant's needs, providing more flexibility during market changes. In addition, creating long-term partnerships rather than temporary deals can foster innovation and continuous improvement in processes, which ultimately benefits customer satisfaction.
Engaging with Cross-Industry Partners
Engaging with partners from different industries offers new perspectives and innovative ideas. By attending industry events and joining professional networks, plant managers can expand their knowledge and learn best practices from other sectors. Such interactions often lead to the discovery of new technologies that can be adapted to enhance production efficiency.
Forming strategic alliances with cross-industry partners can also open doors to new markets. This connectivity brings access to diverse resources and potential collaborations that go beyond the traditional manufacturing environment. By integrating these insights, plant managers can improve processes and create value, driving the plant toward achieving its goals.
Involvement in cross-industry forums can also facilitate valuable exchanges on topics like sustainability and technological advancements, further refining operations and boosting industry relevance.
Preparing for Plant Manager Interviews
Plant manager interviews often focus on identifying leadership abilities, effective communication, and past work achievements. These key areas can demonstrate a candidate’s capability to handle the demands of managing a plant successfully.
Discussing Work Experience and Achievements
Interviewers often want candidates to talk about their past work experiences and achievements. Candidates should provide specific examples of how they improved production or handled challenges in previous roles. Talking about successful initiatives, such as finding ways to reorganize work shifts to eliminate inefficiencies, is crucial. Demonstrating an understanding of utilizing resources effectively can help highlight one's commitment to improvement, as seen in typical interview questions.
Responding to Behavioral Interview Questions
Responding to behavioral interview questions requires candidates to illustrate their problem-solving abilities and decision-making skills under pressure. Sharing experiences where they managed crises or emergencies will show their aptitude in high-pressure situations. It is important to provide detailed stories with clear outcomes, showing they can maintain productivity and safety. Reviewing such targeted interview questions can help candidates prepare effectively.
Showcasing Leadership and Communication
Leadership and communication skills are vital for plant management roles. Candidates should discuss methods they use to foster a positive work environment, such as open-door policies for direct communication and encouraging feedback from employees. Examples where they promoted unity and addressed issues promptly can highlight leadership qualities. A commitment to continuous evaluation and improvement is also essential, helping prospective employers see the candidate as a fit for long-term objectives.
Prioritizing Safety and Compliance
Prioritizing safety and compliance is essential for plant managers. Implementing strict safety measures ensures the well-being of employees and minimizes risks. Conducting regular safety drills and providing comprehensive training are key steps.
Safety regulations play a crucial role. Plant managers must ensure that all operations comply with local, federal, and industry standards. Regular audits and inspections help spot any potential issues early.
Equipment maintenance is vital to maintaining a safe work environment. Scheduling regular check-ups and repairs prevents breakdowns and accidents. Keeping a log of maintenance activities can track the condition of machinery.
Integrating quality control processes into daily operations enhances safety. By monitoring production lines and inspecting products, managers can ensure everything meets safety standards. This process helps in identifying and rectifying defects early on.
A proactive approach to safety fosters a culture of responsibility and vigilance. Encouraging feedback from employees allows for continuous improvement in safety practices. Open communication channels ensure everyone feels empowered to report hazards.
Frequently Asked Questions
When facing challenges in their roles, plant managers often have to use different strategies to maintain a productive and safe environment. These include dealing with conflicts, ensuring team motivation, and improving operations.
Can you describe a challenging situation you faced as a plant manager and how you overcame it?
Plant managers might need to handle unexpected machinery breakdowns or staffing shortages. In these situations, a manager could form a quick-response team to assess and resolve the issue swiftly while keeping all stakeholders informed.
How do you ensure your team stays motivated and productive during periods of high stress or tight deadlines?
Motivation can be maintained by recognizing team achievements and setting clear, attainable goals. Implementing brief daily meetings to track progress and address concerns can boost morale and keep everyone focused.
What strategies do you employ to maintain high safety standards and quality control in a plant environment?
Safety and quality can be ensured by regular audits and training sessions. Plant managers can encourage employees to report any safety concerns immediately and reward teams that consistently meet safety goals. More detailed guidelines can also be found in resources such as Workable's interview questions.
Can you give an example of how you've driven operational improvements within a manufacturing setting?
Operational improvements often involve streamlining processes. For example, a manager might implement a new scheduling system to reduce overtime costs. They might also introduce automated solutions for routine tasks to enhance efficiency, as suggested in plant manager interview discussions.
How do you approach conflict resolution within your team, especially when it involves cross-departmental issues?
Resolving conflicts requires active listening and clear communication. A plant manager could schedule a mediated meeting where all parties can express their views and work together to find a solution. Encouraging an open-door policy can help prevent issues from escalating.
Can you discuss a time when you had to adapt your leadership style to better suit your team's needs?
Leadership styles may need adjustment based on team dynamics. For instance, a manager may shift from a directive to a participative approach to foster more creative input from team members. Such flexibility can significantly improve overall team performance and satisfaction.