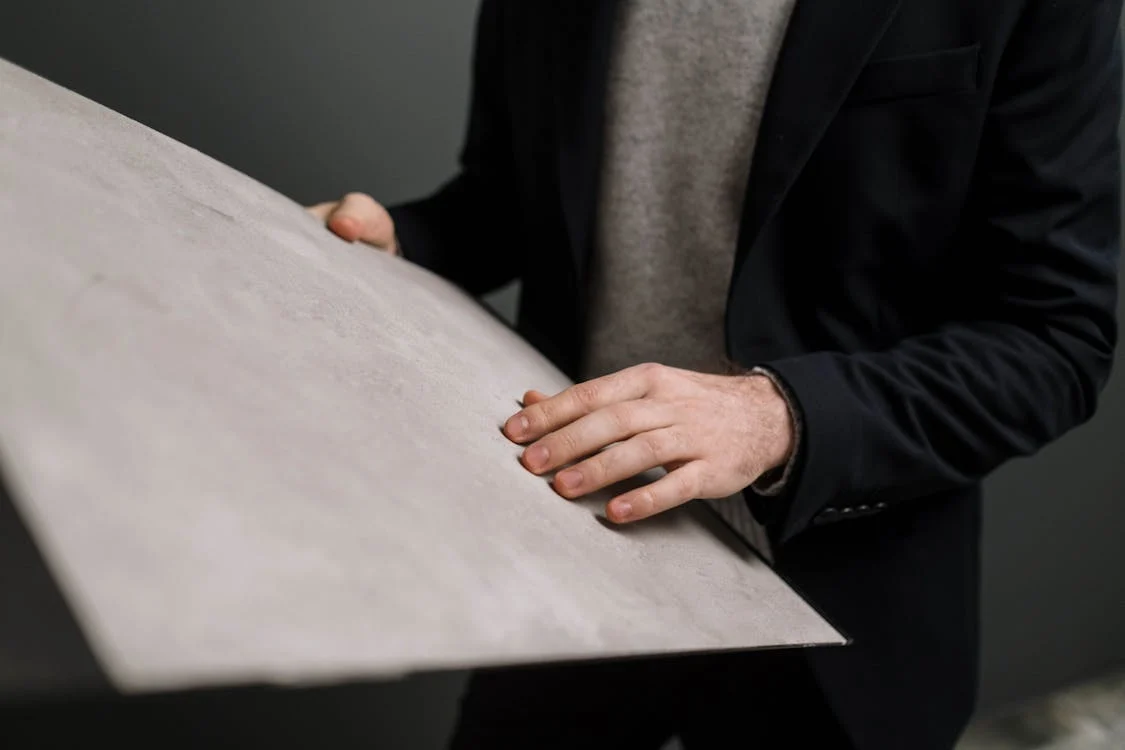
Understanding the Role
Quality Control Managers play a crucial role in ensuring that products or services meet defined quality standards through effective quality management systems. These professionals focus on maintaining high standards of quality by overseeing procedures and staff training.
Core Responsibilities of Quality Control Managers
A Quality Control Manager is tasked with implementing and monitoring quality control processes. They are responsible for inspecting products for defects and ensuring that processes conform to established standards. Regular audits and checks help maintain consistency and reliability in products.
They supervise teams to ensure adherence to quality protocols and collaborate with departments to align quality objectives. They address quality issues by identifying root causes and implementing timely corrective actions, which helps in sustaining product quality and minimizing errors in processes.
Quality Assurance vs Quality Control
Understanding the differences between quality assurance and quality control is essential. Quality assurance is a broad concept focusing on improving and ensuring the quality of processes, which prevents defects from occurring during production.
In contrast, quality control refers to specific activities that are carried out to verify the quality of the final product. It involves actual testing and inspection of products to ensure they meet the set quality standards. While both aim at achieving high-quality standards, quality control is more about detecting problems once they occur and rectifying them then.
Technical Proficiency
A Quality Control Manager must excel in technical elements such as operating quality management systems, adhering to ISO standards, and implementing quality and statistical controls. These skills are critical for maintaining compliance and ensuring effective quality management.
Knowledge of Quality Management Systems
Quality Control Managers should have a thorough understanding of quality management systems (QMS) like ISO 9001. These systems help ensure that procedures align with best practices and regulatory requirements. Familiarity with QMS allows managers to establish and maintain processes that enhance product quality. They must also facilitate internal audits, identifying any discrepancies and areas for improvement. This deep knowledge aids in building a sustainable framework that supports continuous improvement and customer satisfaction.
Familiarity with ISO Standards
ISO standards provide valuable guidelines that are widely recognized in industries worldwide. Managers should be well-versed in relevant standards, such as ISO 9001, which focuses on quality management principles. Knowledge of ISO standards ensures firms meet international benchmarks for efficiency and quality assurance. This familiarity helps identify gaps and implement corrective measures to foster better operational practices. Managers must ensure that all team members are aware of these standards and trained to comply with them.
Quality Control Procedures and Compliance
Implementing strict quality control procedures is crucial for maintaining product reliability and safety. Quality Control Managers must define and document these procedures, ensuring they align with industry policies and regulations. Regular inspections and testing should be performed to maintain high standards and ensure compliance. Managers also need to establish clear reporting systems for tracking quality issues and resolutions. By enforcing stringent controls, they uphold the credibility and brand reputation of their organization.
Statistical Process Control (SPC) Techniques
Statistical Process Control (SPC) techniques use statistical methods to monitor and control production processes. These techniques allow managers to identify variations and prevent defects before they occur. By applying SPC tools, such as control charts, managers can ensure that processes remain within defined limits. This proactive approach reduces waste and improves quality. Mastery in SPC enables managers to drive process improvement initiatives and maintain a high level of quality assurance across operations.
Behavioral Competencies
Quality control managers need strong behavioral skills to ensure product standards meet organizational expectations. These skills include problem-solving, decision-making, leadership, and communication to effectively address quality issues.
Problem-Solving and Root Cause Analysis
Quality control managers often encounter complex issues that require effective problem-solving skills. Identifying and resolving these problems necessitates a thorough root cause analysis. This process involves gathering data, examining potential causes, and determining the primary source of a quality defect. By addressing the root cause, managers can prevent recurring issues, minimizing waste and improving overall product quality.
Tools like Fishbone diagrams and the 5 Whys technique are frequently used for root cause analysis. These methods help break down complex problems into manageable parts, allowing managers to address each component systematically.
Decision Making in Quality Management
Effective decision-making is critical in maintaining high-quality standards. Quality control managers must make informed decisions swiftly to mitigate potential risks. This involves assessing various solutions, weighing their potential outcomes, and selecting the best course of action to ensure product integrity.
Managers often rely on both qualitative and quantitative data to guide their choices. They must remain adaptable to changing circumstances and be prepared to revise decisions when new information arises. This ability ensures that quality issues are promptly addressed, keeping products in alignment with organizational standards.
Leadership and Accountability
Leadership skills in quality management require the ability to motivate and guide a team towards shared goals. Leaders must instill a sense of accountability among team members, ensuring that everyone owns their role in maintaining product quality. This includes setting clear expectations and monitoring performance.
Accountability in quality control means that managers take responsibility not only for their decisions but also for the outcomes. This might involve addressing shortcomings directly and implementing corrective measures quickly to uphold quality.
Communicating Quality Issues
Effective communication skills are essential for discussing quality concerns with stakeholders. Managers must convey complex ideas clearly and concisely, ensuring that everyone understands the nature of the problem and the solutions being implemented.
This involves not only speaking but also listening and responding to feedback from various sources. By fostering open communication, quality control managers can collaborate effectively with other departments, ensuring that quality improvements are a collective effort.
Ultimately, strong communication ensures that quality issues are promptly addressed, maintaining the company's reputation and customer trust.
Managing Processes and Teams
In the role of a Quality Control Manager, successfully managing processes and teams involves focusing on continuous improvement initiatives, establishing and managing quality policies, building strong relationships with suppliers, and demonstrating effective team leadership alongside process control.
Continuous Improvement Initiatives
Quality Control Managers should be proactive in implementing continuous improvement practices. This involves regularly evaluating current processes to identify areas for improvement. They can employ tools like the PDCA (Plan-Do-Check-Act) cycle which helps in making systematic changes.
Engaging team members in brainstorming sessions can also provide valuable insights. By encouraging input, managers foster an environment of collaboration that drives innovation and enhances quality standards.
Setting clear objectives and measuring progress with key performance indicators (KPIs) ensures that all initiatives align with the company’s goals. This focus on continuous improvement can significantly increase efficiency and product quality.
Creating and Managing Quality Policies
Developing comprehensive quality policies is a cornerstone for maintaining high standards. These policies serve as a guide for the entire organization, ensuring consistency across all operations.
Involving team members in the creation of these policies guarantees they understand and adhere to them. This participatory approach also helps to identify potential challenges before they impact the quality.
Regularly reviewing and updating the policies is crucial to adapt to new standards or technologies. A well-documented quality policy highlights the company’s commitment to maintaining high standards and builds credibility with clients and partners.
Relationship Building with Suppliers
Strong relationships with suppliers are key to ensuring product quality. Quality Control Managers must assess suppliers regularly to verify compliance with the established quality standards.
Regular communication with suppliers through meetings or audits helps in resolving any quality issues promptly. Establishing clear quality expectations from the onset prevents misunderstandings and ensures suppliers know what is required.
Negotiating agreements that include quality metrics can hold suppliers accountable. Building a mutually beneficial relationship fosters trust and reliability, which is essential for a steady supply chain and consistent product quality.
Team Leadership and Process Control
Effective team leadership is vital for managing quality control processes. A successful manager knows how to delegate tasks, motivate team members, and resolve conflicts to maintain a harmonious work environment.
Utilizing process control techniques, like Six Sigma, helps in maintaining efficiency and minimizing errors. These techniques rely on data-driven methods to optimize processes and reduce variation.
Training and development programs are essential in equipping the team with skills to handle quality control challenges. Recognizing and celebrating team achievements also boosts morale, ensuring a motivated and focused team committed to upholding quality efforts.
Performance Measurement
Performance measurement is essential for quality control managers to ensure consistent quality and improvement. This involves monitoring quality performance, utilizing customer feedback, conducting internal audits, and implementing corrective action plans. These methods help in maintaining high standards and meeting customer expectations.
Monitoring Quality Performance
Monitoring quality performance involves tracking various metrics to evaluate how well products or services meet established standards. It includes setting benchmarks and regularly comparing actual performance against these benchmarks.
Data analysis plays a crucial role in this process. By examining data trends, managers can identify areas needing improvement. Consistent monitoring helps in catching quality issues early, which prevents larger problems and reduces costs. Regular reports and dashboards can assist in keeping track of performance metrics efficiently, making this process more manageable.
Utilization of Customer Feedback
Utilizing customer feedback is crucial for understanding customer satisfaction and improving quality standards. By collecting and analyzing feedback, managers gain insights into how products are perceived by customers. This information is vital for adjusting processes to better meet customer needs.
Creating effective systems for gathering feedback can involve surveys, direct interactions, or online reviews. Once collected, feedback should be analyzed to identify common themes or issues. Taking customer feedback seriously can lead to higher customer loyalty and improved products.
Conducting Internal Audits
Conducting internal audits involves a systematic examination of processes and procedures to ensure compliance with quality standards. These audits help in identifying weaknesses and areas for improvement within the organization. It requires a detailed plan outlining the scope and objective of the audit.
The audit process may include reviewing documents, inspecting equipment, and interviewing personnel. Findings are documented and evaluated against established standards. Internal audits provide a comprehensive view of the organization’s quality practices and ensure that corrective actions are taken where needed.
Implementing Corrective Action Plans
Implementing corrective action plans involves identifying and addressing problems that arise in quality control processes. These plans are essential for continuous improvement and ensuring that issues do not recur. It starts with accurately identifying the root cause of a problem.
Once the problem is identified, specific actions are outlined to address it. This includes assigning responsibility, setting timelines, and monitoring progress. Corrective actions should be documented and reviewed regularly to ensure effectiveness. Properly executed plans lead to improved quality and enhanced operational efficiency.
Quality Strategy and Vision
Establishing a strong quality strategy involves aligning with business goals and promoting core quality management principles. These strategies ensure that process quality is maintained, non-conformities are minimized, and ongoing process improvement is prioritized.
Aligning with Business Goals
A crucial aspect of a quality strategy is ensuring alignment with the overall business objectives. Quality Control Managers must understand the company's mission and long-term goals to craft a strategy that enhances process quality.
Integrating quality management principles into business operations supports this alignment. This includes ensuring that each department understands its role in maintaining quality standards. Effective communication between departments is vital to ensure that objectives are consistently met and that all team members are working towards the same goals.
Promoting Quality Management Principles
Promotion of quality management principles involves training staff and embedding these principles into daily operations. Emphasizing principles such as process improvement and adherence to standards ensures non-conformities are addressed quickly.
Training programs focused on quality management principles help staff understand and commit to these goals. Constant reinforcement through workshops and regular meetings helps keep these principles front and center.
Monitoring and evaluating processes continuously is essential. Implementing feedback loops and encouraging staff to contribute ideas fosters a culture of quality, making it easier to identify and address any issues quickly.
Targeted Interview Questions
When interviewing for a Quality Control Manager position, employers often use targeted interview questions to evaluate the candidate’s skills and experience. These questions help identify how well a candidate can handle various situations in quality management.
A common question might explore attention to detail. For example, "Can you describe a situation where your attention to detail helped prevent a quality issue?" This type of question ensures the candidate has a keen eye for quality assurance.
Behavioral questions are widely used to see how a candidate has dealt with past challenges. Examples include:
- Describe a time when you had to solve a significant quality issue.
- How have you managed tight deadlines while maintaining quality standards?
- What steps do you take to improve processes?
Quality managers should also be adept at leading teams. Interviewers might ask, "How do you motivate your team to meet quality standards?" or "Can you share how you resolve conflicts within your team?"
Questions that target the candidate's ability to implement systems are crucial. An example question could be, "How would you create an effective system for tracking customer feedback?"
Understanding the range of potential questions can be crucial for quality manager interview preparation. By focusing on past experiences and real-life examples, candidates can effectively demonstrate their capabilities and suitability for the role.
Frequently Asked Questions
Quality control managers often face diverse challenges. These include identifying errors in production, dealing with conflicts, and ensuring smooth transitions when changes occur. Understanding various methods and techniques can enhance their effectiveness in managing quality control.
Can you provide an example of a time when you identified a significant error in the production process and how you resolved it?
Quality control managers play a crucial role in identifying production errors. They might discover a significant issue during routine checks or data analysis. Once identified, they analyze the root cause, implement corrective actions, and monitor the process to prevent recurrence.
How would you handle a situation where there was a conflict between a team member and the established quality control procedures?
Conflicts between team members and procedures can disrupt the workflow. A quality control manager should mediate by discussing concerns with the team member, explaining the importance of procedures, and finding a compromise that maintains quality standards while addressing any valid concerns.
Describe a scenario where you had to implement a major change in the quality control process. What steps did you take to ensure a smooth transition?
Implementing a major change requires careful planning and communication. This involves outlining clear objectives, providing training, and setting up monitoring systems. Continuous feedback and support help the team adapt and ensure the change enhances the quality control process.
Can you discuss your experiences with conducting quality control audits and the outcomes of those audits?
Quality control audits involve assessment of processes to ensure compliance with standards. Through these audits, areas needing improvement can be identified. Successful audits often result in enhanced procedures, reduced errors, and improved overall product quality.
What methods have you found most effective for training staff in new quality control procedures?
Effective training methods include hands-on workshops, visual demonstrations, and regular refresher courses. Combining these with clear documentation ensures that staff fully understand new procedures, enhancing their ability to maintain high quality standards.
How do you evaluate the effectiveness of a quality control system and identify areas for improvement?
Evaluating a quality control system involves regular reviews of performance data and feedback from staff. Key indicators of success include error rates and customer satisfaction levels. By identifying trends and areas for improvement, management can make informed decisions to optimize the system.