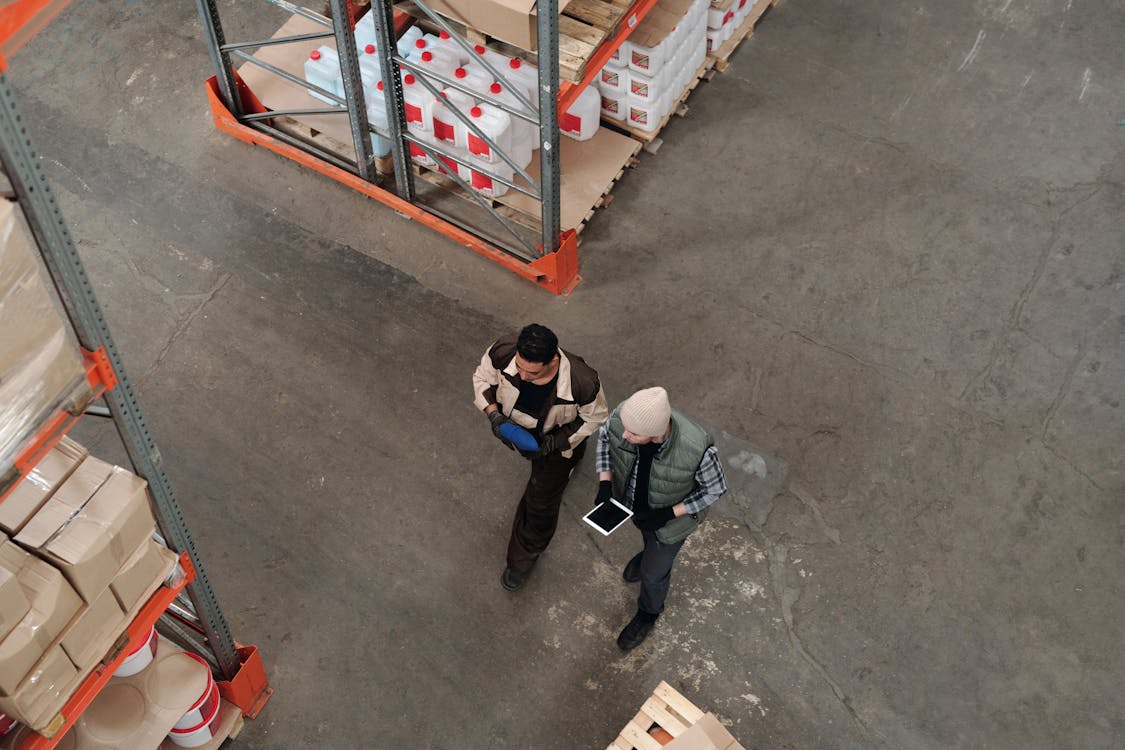
Understanding Warehouse Management
Warehouse management involves a wide array of tasks designed to ensure the efficient movement, storage, and tracking of goods. Key areas include operations, layout optimization, and inventory control.
Fundamentals of Warehouse Operations
Effective warehouse operations are crucial. Processes such as receiving, put-away, picking, packing, and shipping must be streamlined to maximize productivity. Employees should be trained to handle equipment and follow safety protocols to minimize accidents and damages.
Implementing technologies like barcode scanners and warehouse management systems (WMS) can automate tasks and reduce human error. Regular audits and continuous improvement practices ensure that operations remain optimal and adapt to changing demands.
Significance of Efficient Warehouse Layout
An efficient warehouse layout minimizes travel time and maximizes storage space utilization. This involves strategically placing high-turn items closer to packing areas and designing clear paths for forklifts and workers.
Using shelving and racking systems can help optimize vertical space. Properly labeled zones and effective lighting can improve item retrieval speed and safety. Flexibility in layout, such as modular storage units, can accommodate varying inventory sizes and types.
Inventory Management Essentials
Effective inventory management is key for maintaining accurate stock levels and preventing overstock or stockouts. Techniques such as ABC analysis help prioritize items based on their importance and turnover rate.
Cycle counting, rather than annual physical counts, keeps inventory records continuously accurate. Integrating inventory management software with the WMS automates tracking and updates. This ensures real-time visibility and helps in demand forecasting, reducing the risk of surprise shortages or excess inventory.
Role of Technology in Warehousing
The role of technology in warehousing involves various systems and tools that enhance efficiency, accuracy, and productivity. Key technologies include Warehouse Management Systems (WMS) and automation, which streamline operations and reduce errors.
Importance of Warehouse Management Systems (WMS)
Warehouse Management Systems (WMS) are crucial for efficient operations. WMS helps track and manage inventory, optimize storage, and streamline the shipping process. These systems allow warehouse managers to monitor stock levels in real-time, reducing the risk of overstocking or stockouts.
Incorporating WMS can improve barcode scanning and electronic data interchange (EDI), ensuring that data is accurate and up to date. This technology also supports better decision-making by providing detailed reports and analytics. Consequently, this helps in optimizing labor and resources, leading to cost savings and improved customer satisfaction.
Automation and Its Impact on Warehousing
Automation has a significant impact on warehousing by increasing efficiency, reducing labor costs, and minimizing human error. Warehouse automation includes automated guided vehicles (AGVs), robotic picking systems, and conveyor systems.
One key benefit of automation is its effect on inventory management. Automated systems can accurately track inventory levels and locations, making it easier to locate and manage stock. Additionally, automation can enhance the speed and accuracy of order fulfillment, leading to faster delivery times and higher customer satisfaction.
Automation also supports warehouse safety by handling tasks that may be dangerous for human workers, such as heavy lifting. Overall, integrating automation into warehouse operations results in smoother, more efficient processes and improved productivity.
Leadership and Management Skills
Leadership and management skills are crucial for warehouse managers to ensure smooth operations and a productive team environment. These skills include developing organizational strategies, resolving conflicts efficiently, and fostering effective team management and employee training programs.
Developing Organizational Skills
Warehouse managers need robust organizational skills to manage inventory, resources, and workflow. Effective organization minimizes delays and errors in order processing.
Key Strategies:
- Prioritizing tasks: Ensure high-priority shipments are processed first.
- Inventory management: Track stock levels and reorder supplies before running out.
- Workflow optimization: Streamlining processes for efficiency using tools like Gantt charts.
Strong organizational skills streamline operations, improve accuracy, and ensure customer satisfaction.
Conflict Resolution and Management
Conflict can arise in any workplace. Warehouse managers must handle disputes effectively to maintain a harmonious work environment.
Essential Techniques:
- Open communication: Encouraging open dialogue helps address issues before they escalate.
- Active listening: Understanding each party's perspective to find a fair solution.
- Conflict mediation: Acting as a neutral party to facilitate resolutions.
Effective conflict management builds trust and maintains a positive workplace atmosphere.
Fostering Team Management and Employee Training
A warehouse manager's leadership truly shines through team management and training initiatives.
Critical Actions:
- Regular training sessions: Keeping employees updated on safety protocols and best practices.
- Team building activities: Foster camaraderie and cooperation through joint exercises.
- Performance feedback: Provide constructive feedback to help employees improve and grow.
Proactive team management and thorough training boost morale, enhance skills, and drive team success. Enhanced team cohesion leads to more efficient operations and a safer work environment.
By focusing on these key areas, warehouse managers can lead their teams successfully and ensure operational excellence.
Optimizing Warehouse Operations
Optimizing warehouse operations involves enhancing efficiency, implementing continuous improvement processes, and meeting customer satisfaction objectives. These efforts ensure smooth order fulfillment and effective order processing.
Strategies for Maximizing Efficiency
Organize Inventory: Group similar items together. This reduces the time spent searching for products.
Use Technology: Invest in Warehouse Management Systems (WMS) to track inventory and streamline operations. The right system can automate order processing, monitor stock levels, and predict inventory needs.
Optimize Layout: Create a layout that minimizes travel time between storage areas. Consider narrow aisles and taller shelving units to maximize space.
Training: Regular training sessions for staff on best practices and new technologies are vital. This ensures all team members are efficient and up-to-date.
Continuous Improvement Processes
Regular Audits: Conduct audits to identify bottlenecks and inefficiencies. This helps in pinpointing areas that need immediate attention.
Feedback Loop: Encourage employees to provide feedback on daily operations. Their insights can lead to valuable improvements.
Data-Driven Decisions: Use data analytics to monitor performance metrics. Track key performance indicators (KPIs) like pick time, order accuracy, and expedited shipping rates.
Kaizen Methodology: Implement the Kaizen approach for continuous, incremental improvement. This involves small, daily changes rather than large overhauls.
Meeting Customer Satisfaction Objectives
Accurate Order Fulfillment: Ensure that orders are picked, packed, and processed accurately. Mistakes can lead to customer dissatisfaction and returns.
Fast Shipping: Offer options for expedited shipping. Meeting delivery deadlines is crucial for maintaining customer trust.
Customer Communication: Keep customers informed about their order status. Tracking numbers and timely updates improve transparency.
After-Sales Support: Provide excellent customer service post-purchase. Handle returns and complaints efficiently to maintain a positive relationship with customers.
Quality Control: Regularly check products for defects before shipping. Quality control reduces the chances of returns and increases customer satisfaction.
Interview Process for Warehouse Managers
The interview process for warehouse managers focuses on assessing problem-solving skills, leadership and organizational abilities, as well as understanding warehouse safety and compliance. Effective evaluations in these areas are crucial to ensuring candidates are well-suited for the role.
Assessing Problem-Solving Skills
Interviewers often evaluate a candidate's problem-solving skills to ensure they can handle unexpected challenges. Questions may include scenarios involving inventory discrepancies or shipment delays. Candidates should demonstrate their approach to identifying the issue, analyzing possible solutions, and implementing the best course of action.
Example Question: Describe a situation where you had to resolve a significant inventory inaccuracy.
Evaluating Leadership and Organizational Abilities
Leadership and organizational skills are critical for effective warehouse management. Interviewers look for candidates with experience in task delegation, team motivation, and workflow optimization. Questions may focus on past experiences managing staff and coordinating warehouse operations.
Example Question: Can you provide an example of how you improved warehouse efficiency through better organization?
Understanding Warehouse Safety and Compliance
Understanding warehouse safety and compliance is vital for minimizing accidents and ensuring regulatory adherence. Interviewers typically inquire about the candidate's knowledge of safety protocols, handling of hazardous materials, and operation of equipment such as forklifts.
Example Question: How do you ensure compliance with safety regulations and handle hazardous materials in the warehouse?
In summary, assessing these critical skills and knowledge areas ensures the selection of competent warehouse managers who are equipped to handle the various demands of the job.
Data, Metrics, and Performance Analysis
Warehouse managers rely on data to enhance productivity, monitor performance, and maintain accurate inventory levels. Key aspects include understanding the role of data, tracking essential performance metrics, and employing effective inventory control techniques.
The Role of Data in Warehouse Management
Data is crucial in warehouse management as it helps make informed decisions and optimize operations. Managers collect data on various aspects like inventory levels, order fulfillment times, and storage efficiency.
Using data analysis, they can identify trends and issues, allowing them to adjust processes. For example, knowing peak times can help in scheduling more staff. Modern warehouse management systems (WMS) provide real-time data, which aids in quick decision-making and enhances operational efficiency.
Key Performance Metrics for Warehouse Managers
Tracking performance metrics provides insights into a warehouse's efficiency. Important metrics include inventory accuracy, where accurate data on stock levels reduces shortages and overstock. Order fulfillment time, the time taken to pick, pack, and ship an order, is another key metric influencing customer satisfaction.
Other significant metrics include cycle counting accuracy—a technique to maintain inventory accuracy—and space utilization, which measures how effectively warehouse space is used. Monitoring these metrics helps managers pinpoint areas needing improvement and optimize operations.
Inventory Control Techniques
Effective inventory control is essential for a well-functioning warehouse. Techniques like ABC analysis help prioritize inventory based on the value and frequency of use. Items are classified into three categories:
- A items: High value, low quantity
- B items: Moderate value and quantity
- C items: Low value, high quantity
Cycle counting is another technique that maintains inventory accuracy without the need for full stock takes. This method involves counting a small portion of inventory regularly.
By focusing on specific items, discrepancies can be identified and corrected quickly, ensuring that inventory data remains reliable and useful for decision-making.
Challenges and Stress Management
Warehouse managers often face pressure from tight deadlines, changes in operations, and the need to optimize efficiency. Effective stress management is critical to maintaining a productive and safe work environment.
Handling Pressure and Deadlines in Warehousing
Warehouse managers frequently deal with high-pressure situations due to deadlines or unexpected order surges. To handle this pressure, they prioritize tasks effectively and delegate responsibilities.
Creating a schedule that allows for flexibility can help managers accommodate last-minute changes. They also implement time-saving technologies like warehouse management systems (WMS) to improve accuracy and reduce the time spent on manual tasks.
Effective communication with staff is crucial. Regular check-ins and updates help ensure everyone is aligned with the goals.
Additionally, providing staff with training on handling stress can create a more resilient workforce.
Change Management and Navigating Transitions
Change is inevitable in warehousing, whether due to new technology, processes, or organizational structures. Managers play a key role in steering their teams through these transitions.
They do so by planning thoroughly and preparing staff well in advance of any changes.
Transparent communication is vital during transitions. Managers should clearly explain the reasons for the changes, the expected impacts, and the benefits. This helps reduce resistance and anxiety among the team members.
Moreover, involving employees in decision-making can increase buy-in and smooth the transition process. Managers also focus on training and support, ensuring employees have the necessary skills to adapt to new systems quickly.
Redesigning and Reorganization Strategies
Inefficiencies in a warehouse can lead to time losses and increased stress levels. Managers need to periodically assess and redesign workflows to streamline operations.
Reorganization strategies often involve reshuffling the layout to optimize storage and retrieval times. This includes using tools like ABC analysis to categorize inventory based on importance and frequency of use.
Investing in ergonomics can also improve efficiency and reduce physical strain on employees. For example, automating heavy lifting tasks can minimize injury risks.
Continuous improvement is key. Managers should regularly collect and analyze data on warehouse performance, making incremental changes to remain efficient and agile.
To support these strategies, it's essential to foster a culture of adaptability and continuous learning within the team, ensuring the workforce is always prepared to handle changes and improvements efficiently.
Training and Development
Training and development are crucial for warehouse managers to ensure their teams perform efficiently and safely. Regular employee training helps staff stay updated with new processes and technologies.
For instance, training on operating a forklift can significantly reduce workplace accidents. Well-trained personnel can handle equipment more effectively, ensuring better productivity and safety.
Warehouse managers should focus on continuous development through workshops and certification programs. They might consider online courses or on-site training sessions to cater to different learning preferences.
A significant part of development is also fostering soft skills. Encouraging teamwork, communication, and problem-solving can create a more collaborative work environment.
Here’s a brief look at some training areas:
Training AreaPurposeForklift OperationSafe and efficient handling of forkliftsSafety ProtocolsReducing workplace accidents and injuriesInventory ManagementAccurate and efficient stock handlingTeam LeadershipImproving team collaboration and management
Investing in employee training also boosts morale. Employees feel valued and are more likely to stay long-term. Hence, a focus on training fosters a more competent and committed workforce.
For more insights, you can explore interview questions about training and development, which highlight the importance of continuous learning.
Logistics and Supply Chain Integration
Efficient integration of logistics and supply chain processes is critical for warehouse management success. It ensures the smooth receipt and dispatch of goods, optimizing overall distribution. Key areas of focus include:
Logistics Coordination
Warehouse managers must oversee the coordination of logistics to ensure timely delivery of products. This involves close monitoring of transportation schedules, managing inventory levels, and tracking shipments.
Supply Chain Management
Effective supply chain management involves implementing strategies that streamline operations from suppliers to customers. Managers must ensure that all elements of the supply chain, including procurement, production, and distribution, work seamlessly together.
Technology Integration
Using advanced technologies like Warehouse Management Systems (WMS) and Supply Chain Management (SCM) software helps in managing complex operations. These technologies provide real-time data and analytics to improve decision-making processes.
Collaboration with UPS and Other Carriers
Collaborating with carriers like UPS ensures reliable and efficient transportation of goods. Managers must negotiate contracts, monitor carrier performance, and resolve any delivery issues that arise.
Process Optimization
Optimizing warehouse processes includes improving the layout for better movement of goods, enhancing picking and packing methods, and reducing handling times. This leads to improved efficiency and customer satisfaction.
Inventory Management
Maintaining accurate inventory levels is crucial. This involves regular cycle counts, real-time inventory updates, and using automated systems to minimize errors and discrepancies.
By focusing on these areas, warehouse managers can achieve better logistics and supply chain integration, leading to increased operational efficiency and reduced costs.
Enhancing Communication and Problem-Solving
Effective communication and problem-solving are vital for warehouse managers. These skills ensure smooth operations and timely resolution of issues.
Communication involves clearly conveying expectations and updates to the team. Frequent check-ins can help maintain clarity. Strong communication reduces errors and boosts productivity.
Problem-solving skills are crucial in a warehouse setting. Managers must address unexpected issues swiftly. This requires critical thinking and a calm approach.
Common interview questions for assessing these skills include:
- "Describe a time when you had to solve a problem without managerial guidance."
- "How do you handle communication breakdowns within your team?"
Conflict resolution is another key area. Managers often deal with disputes among staff. Techniques such as active listening and mediation are essential.
Understanding operational procedures helps in identifying potential problems before they escalate. Familiarity with protocols ensures quick and effective solutions.
Table: Key Skills and Questions
SkillSample Interview QuestionCommunication"Give an example of how you ensured clear communication in your last role."Problem-solving"Describe a challenging problem you solved in your previous job."Conflict Resolution"How do you handle conflicts among team members?"
This approach ensures that candidates possess the necessary abilities to handle the dynamic environment of a warehouse efficiently.
Cost-Effectiveness and Resource Management
Focusing on cost-effectiveness and resource management is crucial for warehouse managers. They must implement cost-saving measures to ensure smooth operations while minimizing expenses.
Key Areas to Consider:
- Order Processing: Streamline order processing to reduce errors and speed up fulfillment times. Automation tools can help in managing orders more efficiently, reducing manual labor costs.
- Resource Allocation: Efficient use of resources like labor and equipment. Cross-training employees can provide flexibility, allowing workers to handle multiple tasks and minimizing downtime.
- Inventory Management: Effective inventory management is vital. Keeping track of stock levels prevents overstocking and understocking issues. Implementing a just-in-time (JIT) inventory system can lead to significant cost savings.
Additional Measures:
- Bulk Purchasing: Turning to bulk purchasing can result in substantial discounts on supplies, helping to cut down costs.
- Energy Efficiency: Utilizing energy-efficient lighting and equipment can save on utility bills.
- Preventive Maintenance: Regular maintenance of machinery and equipment can extend their lifespan and prevent costly repairs.
Examples:
- A warehouse manager might recognize potential savings by using automated order processing tools, thus improving efficiency and reducing the number of manual errors.
- By cross-training staff, managers can manage workloads more flexibly, leading to better use of available resources.
These strategies can help warehouse managers achieve a more cost-effective and resourceful operation.
Frequently Asked Questions
Warehouse managers often face complex challenges. Here are key questions and answers to understand how they handle various situations and responsibilities.
Can you describe a time when you effectively managed your team through a challenging project?
Managers often recount situations where they coordinated multiple tasks, set clear goals, and maintained open communication with their teams. They highlight problem-solving techniques and emphasize the importance of teamwork and accountability.
How do you prioritize tasks and delegate responsibilities in a warehouse environment?
Warehouse managers discuss how they assess task urgency and importance, often using tools like task lists or software. They explain their approach to assigning tasks based on employees' strengths and skills, ensuring efficiency and productivity.
Tell us about a situation where you had to make a tough decision that affected your entire team.
In describing such scenarios, managers typically talk about weighing the pros and cons of their options. They often focus on clear communication, transparency, and ensuring that the team's morale and trust are maintained even during tough decisions.
What strategies do you employ to maintain a safe and productive warehouse?
Safety and productivity are essential in warehouse management. Managers share their methods, including regular safety audits, employee training sessions, and proper equipment maintenance. They also stress the need for clear safety protocols and constant vigilance.
Describe a scenario where you identified a problem in the warehouse and how you resolved it.
Managers often face issues like inventory discrepancies or workflow bottlenecks. They explain how they identified the root cause of the problem, implemented corrective measures, and monitored the situation to ensure the problem was resolved effectively.
How do you ensure that warehouse operations align with the overall objectives of the company?
Alignment with company objectives involves understanding broader goals and integrating them into daily operations. Managers discuss how they use key performance indicators (KPIs), regular meetings with senior management, and strategic planning to keep warehouse operations on track.