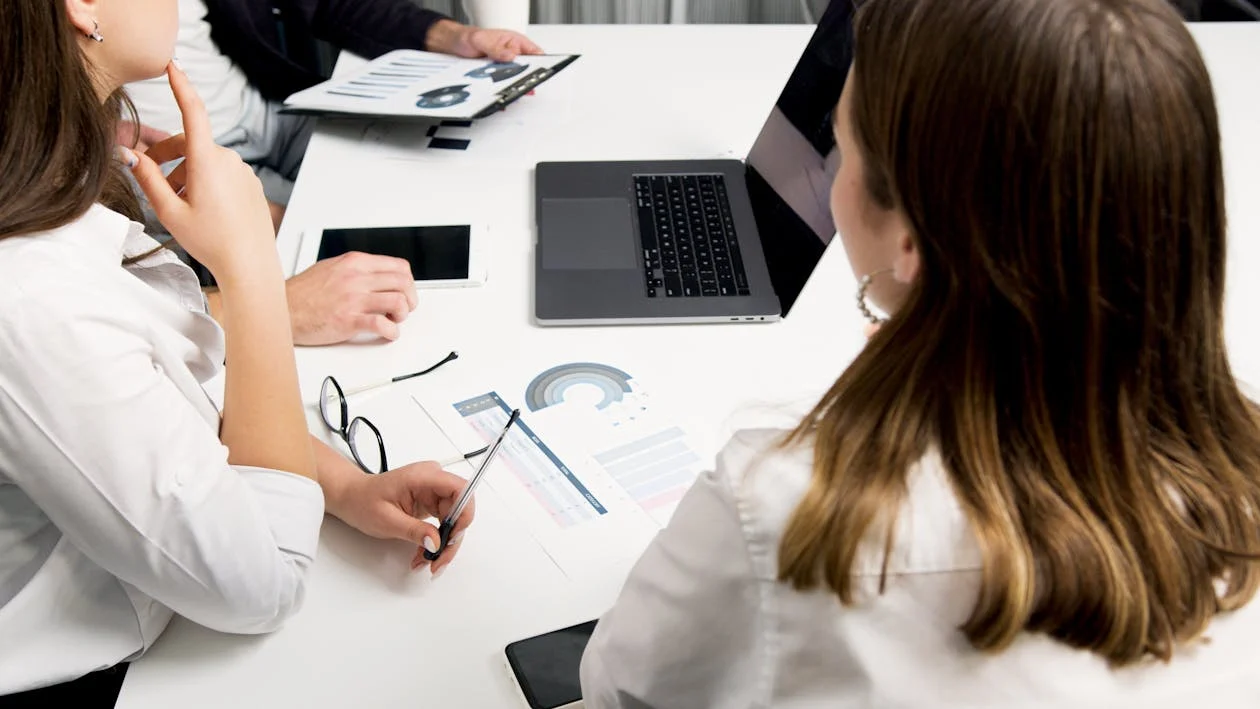
Understanding Quality Control in Manufacturing
Quality control in manufacturing ensures that products meet set quality standards and comply with regulations. This process involves a robust quality management system (QMS) that helps identify defects and maintain consistency in production. Quality control managers play a crucial role in overseeing these operations and ensuring adherence to standards.
Fundamentals of Quality Management
Quality management revolves around integrating processes that improve product consistency. Key practices include inspecting products at various stages and utilizing tools like digital calipers and automated systems. These practices focus on maintaining high-quality standards throughout production by implementing continuous monitoring and proactive problem-solving.
Systems like Six Sigma and Total Quality Management (TQM) often come into play. Six Sigma focuses on minimizing defects through data-driven approaches. TQM, on the other hand, emphasizes company-wide commitment to quality.
Importance of Compliance to Quality Standards
Compliance with quality standards is vital for meeting customer expectations and regulatory demands. Standards such as ISO 9001:2015 offer frameworks to help manufacturers ensure quality. These standards outline specific processes and criteria that products should meet.
By aligning with these established standards, companies can enhance their market reputation and customer trust. Moreover, compliance reduces waste, optimizes resource usage, and prevents costly recalls. These benefits contribute to sustainability and long-term success in the manufacturing sector.
Role of Quality Control Managers
Quality control managers are pivotal in maintaining the quality management system. They oversee quality control procedures and ensure that products meet required standards. These managers are responsible for implementing quality control tools and coordinating with other departments to achieve desired outcomes.
They also train staff to monitor quality effectively and create reports for continuous improvement. By addressing issues proactively, they help the company meet both internal and external expectations. Good management involves a detailed understanding of quality parameters and regulatory standards, ensuring that all manufacturing processes align with business goals.
Strategies for Effective Quality Control
An effective quality control strategy can greatly enhance product quality and customer satisfaction. By developing a comprehensive process, implementing Total Quality Management, and applying statistical methods, quality managers can ensure continuous improvement and effective controls.
Developing a Quality Control Process
Developing a strong quality control process is critical for any organization. First, it involves quality planning, where objectives and quality standards are set. Managers must identify key performance indicators to measure success. Clear documentation of procedures helps maintain consistency in quality control activities, minimizing errors and inefficiencies.
Involving staff at all levels encourages a shared commitment to meeting quality standards. Regular training ensures that team members understand their roles and responsibilities. Periodic audits and reviews of the process help identify areas for improvement, allowing for timely adjustments and fostering continuous improvement in quality practices.
Implementing Total Quality Management (TQM)
Total Quality Management (TQM) is an approach that focuses on long-term success by enhancing customer satisfaction. It involves all employees in quality improvement activities, creating a culture where quality is a shared responsibility. Each team member is encouraged to contribute to quality improvement.
Leadership commitment is crucial in TQM. Leaders must drive the initiative by promoting an organization-wide focus on quality. Tools like quality registers can help track and document quality management activities. TQM also emphasizes customer feedback to align products with customer needs.
Continuous improvement is a core principle of TQM. Strategies should be regularly updated based on feedback, testing, and technological advancements, ensuring ongoing enhancement of processes and products.
Applying Statistical Process Control
Statistical Process Control (SPC) is a method used to monitor and control a process through data. SPC involves collecting data from processes and using statistical methods to identify process variations and their sources. It helps in maintaining process consistency and quality output.
Key tools in SPC include control charts, which are graphical representations of data that help detect variations within the process. Using these charts enables managers to determine if a process is in control or if corrective actions are needed. Data-driven insights from SPC allow for informed decision-making, aiding in quality improvement strategies.
Implementing SPC fosters a proactive approach to problem-solving and supports continuous improvement by targeting potential issues before they impact product quality.
Designing and Using Quality Control Charts and Tools
Successful quality control relies on selecting the right techniques and integrating methodologies like Six Sigma. Utilizing statistical quality control enhances the ability to measure and analyze key quality metrics.
Selecting Appropriate Quality Control Techniques
Choosing the right quality control techniques is crucial. Quality control managers should begin by identifying the most relevant quality metrics for their processes. These might include factors like defect rates, cycle time, or yield rates. Techniques like cause-and-effect diagrams, check sheets, and Pareto charts can help identify potential problem areas and prioritize improvement efforts.
For instance, Pareto charts are beneficial for visualizing the most common issues and focusing on areas that will yield significant improvements. On the other hand, control charts help in monitoring process stability over time, making it easier to spot variations that require corrective actions. A mixed approach, using both these tools and others like scatter diagrams, ensures a comprehensive assessment.
Integrating Six Sigma Methodology
Six Sigma is a method designed to improve quality by reducing variability in processes. It emphasizes the use of data and statistical analysis to measure and improve operational performance. By integrating Six Sigma, companies can aim for near perfection through a systematic approach that reduces defects.
Six Sigma utilizes a structured process known as DMAIC (Define, Measure, Analyze, Improve, Control). Each phase plays a pivotal role in identifying inefficiencies and implementing solutions. The Measure phase, for example, involves collecting data pertinent to quality metrics and using process maps to understand workflow intricacies. This data is analyzed statistically to identify areas for improvement. Once changes are implemented, they must be controlled to ensure ongoing efficiency and quality.
Leveraging Statistical Quality Control
Statistical quality control uses various statistical methods to monitor and maintain the quality of products and services. It involves applying statistical techniques like sampling and hypothesis testing to detect and correct any issues in the production process.
Control charts are a primary tool in statistical quality control, helping managers visualize data and identify trends or deviations from expected performance levels. Another important tool is the histogram, which provides a graphical representation of data distributions, aiding in quick analysis.
Managers can utilize these tools to set limits and ensure processes operate within acceptable parameters. By consistently applying these methods, companies can ensure their products meet quality standards and customer expectations effectively.
Best Practices for Inspection and Testing
Quality control managers must handle inspections and testing with precision to ensure high product standards. These processes are crucial in identifying defects and maintaining regulatory compliance, especially in fields like pharmaceutical quality control. Effective management, optimized testing, and thorough audits are key to successful outcomes.
Managing Inspections Effectively
Effective inspection management requires a structured approach. One of the first steps is to set clear inspection criteria, which serve as benchmarks for quality. Managers should ensure that the inspection team understands these standards thoroughly.
Pre-inspection training is essential. A well-prepared team knows what to look for and can efficiently identify non-compliance or defects. Regular quality audit sessions help teams stay up-to-date with standards and procedures, fostering consistency.
Using technology enhances inspection efficiency. Digital tools can streamline documentation, making it easier to track results and trends. This approach not only saves time but also minimizes human error, leading to more reliable inspections.
Optimizing Testing Procedures
To optimize testing procedures, it is vital to maintain equipment in tip-top shape. Regular calibration of testing tools ensures accuracy and consistency. This is especially crucial in pharmaceutical quality control, where precision is non-negotiable.
Testing procedures should be standardized. Standardization allows for repeatability and reliability across different testing teams and locations. Documenting every step of the process helps in identifying areas for improvement and addressing inconsistencies.
Leveraging automation can boost efficiency significantly. Automated systems allow for high-volume testing with minimal errors and enable quick response to any discrepancies found. This ensures products meet quality standards before reaching consumers.
Quality Audit and Review
Regular quality audits and reviews are essential in maintaining high standards. Audits provide a comprehensive assessment of both inspections and testing processes. They identify weak points and suggest corrective actions, ensuring continuous improvement.
Incorporating feedback from audits into action plans can greatly enhance quality control measures. It is important to involve all stakeholders in reviewing current practices. Their insights can lead to innovations and improvements in the process.
Quality audits should not focus solely on finding faults. They should also recognize successful practices and encourage their consistent implementation. This balanced approach promotes a positive quality culture within the organization.
Fostering a Culture of Quality and Teamwork
Quality control managers play an essential role in strengthening teamwork and establishing a robust culture of quality. By focusing on forming dedicated teams, creating structured quality circles, and actively involving employees, organizations can achieve significant improvements in quality.
Building Quality Assurance Teams
Building effective quality assurance teams is crucial for a successful quality culture. These teams should be diverse, bringing together individuals with varied skills and perspectives to encourage innovative solutions and comprehensive problem-solving.
Quality assurance teams often work closely with standards like ISO 9000, which provide guidelines for maintaining consistent quality. It is important to ensure team members are well-trained and informed about these standards, fostering a shared understanding of quality objectives.
Regular training and skill development sessions should be conducted to keep the teams updated with the latest industry practices. This not only boosts confidence but also supports the continuous improvement of quality management processes. Teams should be empowered to take ownership of their tasks, fostering a sense of accountability and motivation.
Establishing Quality Circles
Quality circles are small groups of employees who meet regularly to identify, discuss, and solve work-related problems. These circles provide a structured way to engage employees in quality improvement initiatives.
By implementing quality circles, organizations can tap into the collective knowledge and experience of their workforce. Encouraging open discussions and brainstorming sessions helps uncover root causes of issues and develop effective strategies for improvement.
These circles should be supported by management, with access to resources and time to dedicate to their tasks. Recognition of contributions and achievements within quality circles can further incentivize participation and reinforce the importance of a quality-oriented culture. This approach promotes collaboration and helps embed quality practices throughout an organization.
Encouraging Employee Involvement
Employee involvement is vital for fostering a quality culture where everyone contributes to quality improvement. Encouraging participation at all levels ensures that employees feel valued and integral to the organization’s success.
Opportunities for employees to voice their ideas and concerns should be consistently provided. Regular feedback sessions and suggestion programs can be effective in garnering input from employees. Involving employees in decision-making processes related to quality improvement can enhance commitment and ownership.
Training and development initiatives tailored for employees can further empower them with the skills needed to identify and address quality issues proactively. This approach not only boosts morale but also nurtures a more dedicated and quality-focused workforce.
Creating Effective Quality Control Presentations
Quality control managers can significantly enhance their presentations by focusing on informative design, effective use of infographics, and clear data presentation. Employing tailored PowerPoint templates and utilizing editable slides can make complex information more accessible and engaging for the audience.
Designing Informative PowerPoint Templates
Designing PowerPoint templates that are both informative and visually appealing is crucial. Managers should consider templates that allow for organized data presentation while maintaining a clean aesthetic. Templates should include sections for text, bullet points, and visuals like charts and diagrams.
It's essential to maintain a balance between text and visuals. Overloading slides with information can overwhelm the audience, so consider using bullet points and concise descriptions. Using color schemes that complement the company's branding can also enhance recognition and engagement.
Utilizing Infographics and Editable Slides
Infographics are powerful tools for conveying information quickly and effectively. Quality control managers should leverage infographics to illustrate key points, trends, or processes in a visually engaging way. Editable slides allow for adjustments to infographics, ensuring they accurately represent current data.
It's important that infographics are straightforward and not cluttered. Use icons and symbols sparingly to avoid confusion. Editable slides offer flexibility. They allow managers to tailor the presentation to different audiences or update information as needed.
Presenting Data with Clarity
When presenting data, clarity is paramount. Use tables and graphs to highlight important statistics and trends. Choose the right type of graph for the data, such as pie charts for proportions or line graphs for trends over time.
Data should be labeled clearly, and axes should be visible and correctly titled. Providing a brief explanation alongside visuals can help the audience grasp complex information. Keeping slides free from jargon ensures clarity and understanding, allowing attendees to follow along without confusion.
Continuous Improvement and Innovation in Quality Control
Continuous improvement is essential in quality control, focusing on ongoing enhancements to products and processes. It encourages a culture where feedback is valued, leading to better problem-solving strategies.
Quality improvement involves specific actions to boost efficiency. This may include analyzing performance metrics, implementing corrective actions, and fostering open communication among team members.
Key Strategies for Continuous Improvement:
- Regular feedback sessions
- Data-driven decision-making
- Consistent training and development
Innovation in quality control involves adopting new methods and tools to improve outcomes. Techniques like the Plan-Do-Check-Act (PDCA) cycle can streamline processes. Using quality circles, small groups can work collaboratively to address challenges and implement solutions. For more information, see the Ultimate Guide to Continuous Improvement.
Benefits of Continuous Improvement:
- Reduced errors
- Increased efficiency
- Enhanced employee engagement
Adopting innovative approaches helps in maintaining high standards. Techniques such as Kaizen and the Juran Trilogy, which includes quality planning, control, and improvement, support these goals. Learn about these methods in Continuous Process Improvement resources.
By focusing on continuous improvement and fostering an environment open to innovation, quality control managers can ensure lasting success and resilience in their organizations.
Impact of Quality Control on Business Outcomes
Quality control has a profound impact on various aspects of business performance. By focusing on specific areas such as customer satisfaction and cost management, businesses can see significant improvements in their overall operations. Each focus area highlights the undeniable benefits that quality control brings to an organization.
Enhancing Customer Satisfaction and Focus
Quality control plays an important role in boosting customer satisfaction. Businesses that consistently deliver high-quality products or services are seen as reliable. This reliability strengthens customer loyalty and trust. An emphasis on customer focus helps companies tailor their offerings to meet the demands and preferences of their clients. Happy customers are more likely to give positive reviews and recommend the business to others.
By implementing thorough quality control procedures, businesses can actively reduce product defects and service errors. This attention to detail reassures customers that they are receiving top-tier products. Moreover, companies that listen to feedback and make improvements are well-regarded by their community, further cementing their place as leaders in customer satisfaction.
Achieving Competitive Advantage through Quality
Quality control is a key factor in securing a strong competitive advantage. Companies that prioritize quality are often able to stand out in saturated markets. Enhanced quality leads to unique branding opportunities and the ability to set higher price points. Loyal customers are less likely to switch to competitors, ensuring steady revenue streams.
Additionally, businesses focusing on quality control can adapt more swiftly to industry changes. With robust management frameworks in place, they can efficiently roll out new products or services. This adaptability provides a strategic edge, especially in industries marked by rapid innovation. Leadership in quality control positions businesses as market leaders.
Cost Reduction and Supply Chain Management
Implementing rigorous quality control measures can lead to significant cost reductions. Efficient quality control helps identify and eliminate waste, faulty processes, and inefficiencies in the production line. This not only lowers production costs but also decreases the likelihood of recalls or warranty claims, which can be costly for businesses.
Supply chain management benefits greatly from quality control. With a structured approach, companies can work closely with suppliers to ensure that materials meet expected standards. This collaboration fosters strong relationships with suppliers, contributing to streamlined operations. Quality assurance at every stage ensures cost-effective and reliable supply chain management.
Frequently Asked Questions
Quality Control Managers face unique challenges when presenting to teams and stakeholders. The questions addressed below include practical advice on improving presentation skills and strategies for effective communication of quality objectives.
How can I improve my presentation skills as a Quality Control Manager?
To enhance presentation skills, practice regularly and seek feedback. Focus on clarity and conciseness in presentations. Engaging the audience by asking open-ended questions helps maintain interest. Use body language and eye contact to convey confidence.
What strategies are effective for a Quality Control Manager to communicate quality objectives to a team?
In communicating quality objectives, it's important to be clear and direct. Setting specific goals and using examples helps illustrate quality standards. Regular team meetings and open communication foster understanding and alignment with objectives. Creating a feedback loop encourages team participation.
In what ways can a Quality Control Manager ensure consistency during team presentations?
Preparation is key to consistency. Developing a standard template for slides and notes can help. Rehearse the presentation to minimize errors and ensure a smooth delivery. Consistency in message and tone should align with company culture and values.
Which key points should be emphasized in a Quality Control presentation to align with best practices?
Emphasizing data-driven outcomes, customer feedback, and continuous improvement are crucial. Communicate the impact of quality measures on business success. Align presentations with industry standards and highlight the role of each team member in achieving quality goals.
How can Quality Control Managers effectively use Powerpoint to convey their message?
To effectively use PowerPoint, keep slides simple and focused. Limit the amount of text and use visuals to support key points. Use charts and graphs to illustrate data clearly. Ensure readability by choosing appropriate fonts and colors.
What are the core responsibilities of a Quality Control Manager when presenting to stakeholders?
When presenting to stakeholders, a Quality Control Manager should clearly define the purpose and goals of the presentation. Effective communication of risks, opportunities, and the impact of quality initiatives is essential. Building trust through transparency and honesty is critical for successful stakeholder engagement.