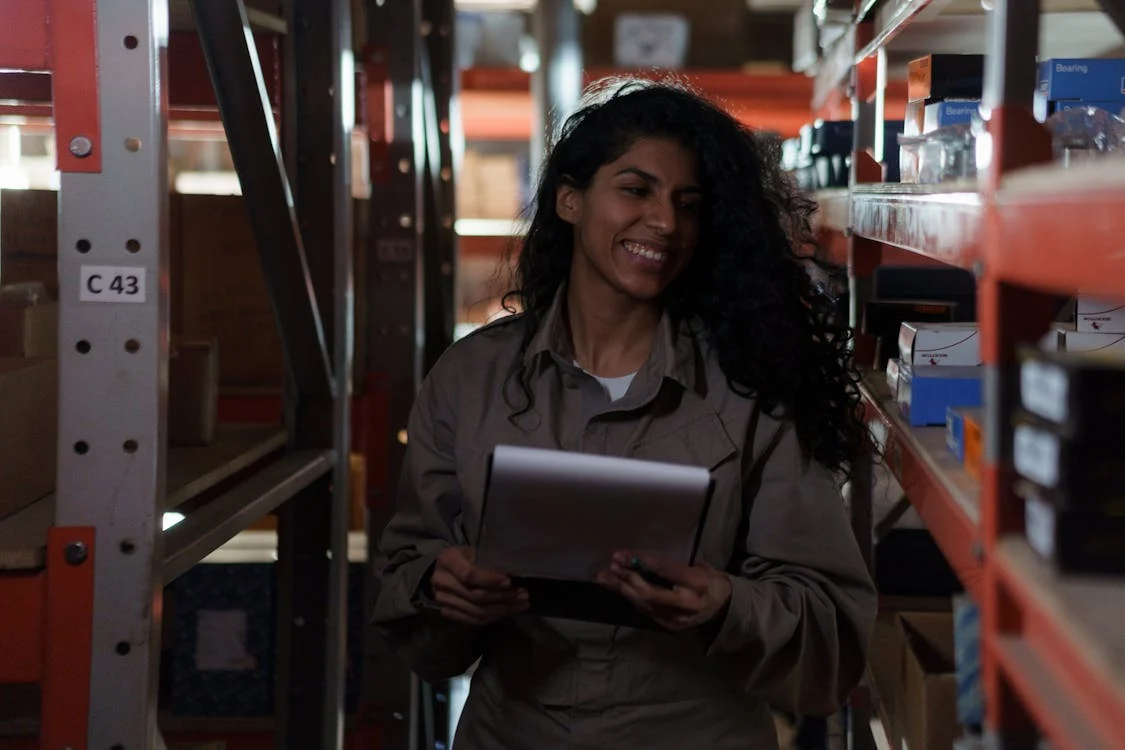
Understanding Warehouse Management
Warehouse management is essential for efficient supply chain operations. By focusing on warehouse operations, technology, and inventory control, businesses can ensure smooth processes and maximize productivity.
Warehouse Operations and Their Significance
Warehouse operations involve the day-to-day activities that keep a warehouse running efficiently. These include receiving goods, storing inventory, picking and packing orders, and shipping products. Each step is crucial for timely delivery and customer satisfaction. Effective warehouse management cuts costs and boosts workflow by reducing errors and optimizing space.
Technology plays a big role in enhancing warehouse operations. Automated systems like conveyors and sorters speed up processes and reduce manual labor. Real-time data helps managers track inventory levels, adjust orders, and prevent stockouts. With the right tools, warehouses become more productive and cost-effective.
Key Aspects of Warehouse Management Systems (WMS)
A Warehouse Management System (WMS) is software designed to optimize warehouse operations. It helps coordinate tasks such as inventory management, order fulfillment, and labor allocation. A WMS provides visibility into stock levels, allowing managers to make informed decisions about restocking and space utilization.
The technology integrates with enterprise systems, providing seamless operations from order receipt to delivery. Real-time data from a WMS reduces errors and improves efficiency. Some systems offer advanced features like automated picking, barcode scanning, and route optimization, streamlining processes and saving time. Investing in a reliable WMS enhances overall warehouse performance and customer satisfaction.
Principles of Inventory Management
Inventory management involves maintaining the right balance of stock to meet demand without overstocking. Effective management reduces costs and minimizes wastage. Key principles include accurate inventory tracking, demand forecasting, and reorder point calculation.
Technology, like RFID and barcoding, offers precise tracking and faster inventory checks. Regular audits and cycle counts prevent discrepancies, ensuring accurate stock levels.
Effective inventory control involves setting appropriate safety stocks and lead times. With these strategies, warehouses can meet customer needs promptly. Understanding and implementing these principles keeps inventory levels optimized and supports smooth warehouse operations.
Optimizing Warehouse Layout and Operations
Improving warehouse operations starts with a smart layout. It caters to more than organization; it enhances workflow and maximizes space utilization. Streamlining order fulfillment and employing technology also play crucial roles in boosting productivity.
Designing an Effective Warehouse Layout
An efficient warehouse layout is a foundation for smooth operations. It begins with a space assessment to understand room for inventory and operational paths. Optimizing involves clear aisles for easy access, strategically placing high-demand items within reach, and minimizing unnecessary movements.
Organized storage like pallet racks or shelves can enhance space usage. Proper labeling and signage guide employees, saving time during picking. Safety should not be overlooked—routes should be free from obstructions to ensure secure movement.
Streamlining Order Fulfillment Processes
Streamlining order fulfillment involves refining every step of the process. Effective picking strategies like batch picking or zone picking can speed up order gathering. Automated sorting systems assist in organizing orders efficiently.
Efficient packaging stations reduce delays, and clear documentation speeds up shipping. Good communication between departments is vital to prevent bottlenecks. Regularly reviewing and updating processes ensures they remain effective and efficient.
Leveraging Technology for Improved Stock Management
Technology solutions are key in optimizing stock management. Using warehouse management systems (WMS) helps track inventory in real-time. This reduces stock discrepancies and enhances accuracy.
Automated systems aid in monitoring stock levels, preventing overstock or stockouts. Barcode scanners and RFID systems facilitate quick item identification. Data analytics can predict demand, enabling better stock planning and replenishment.
Strategic use of technology boosts productivity and efficiency. It provides valuable insights into warehouse operations, allowing for continuous improvement. Warehouse managers should consider integrating these tools to stay competitive.
Incorporating Advanced Technology in Warehousing
Advanced technology is changing warehouse management significantly. The focus is on improving productivity, increasing visibility, and learning from real-life examples of technological upgrades. Using automation, cutting-edge technologies, and case studies can help illustrate these advancements.
Automation and Its Impact on Productivity
Automation is revolutionizing warehouse operations. Implementing an automated warehouse order picking system enhances efficiency by speeding up order fulfillment and reducing human error. Automated systems can handle repetitive tasks like sorting and stacking, freeing up workers for more complex duties.
Key Benefits of Automation:
- Reduces labor costs
- Increases order accuracy
- Boosts overall productivity
Additionally, technologies like robotic systems and drones can streamline inventory management by ensuring items are consistently tracked and accurately counted, thus maintaining inventory levels efficiently.
Enhancing Visibility with Cutting-Edge Technologies
Visibility in warehouses is enhanced through the use of advanced technology solutions. Barcode scanning and Radio Frequency Identification (RFID) are essential tools for real-time tracking of goods throughout the supply chain. They significantly improve data accuracy, ensuring that inventory levels are precisely monitored and managed.
Advantages of Enhanced Visibility:
- Real-time data access
- Improved inventory accuracy
- Faster response times to market changes
Integrating data analysis tools allows managers to make informed decisions, optimize storage space, and improve overall warehouse efficiency. By using these technologies, warehouses can adapt to demand changes quickly and efficiently.
Case Studies: Warehouse Technological Upgrades
Several case studies highlight successful integrations of technology in warehousing. For instance, a company utilizing RFID systems saw a 30% increase in inventory accuracy within six months. Another example includes a facility that adopted automated picking systems and reduced order processing times by 40%.
These cases underline the importance of embracing new technology. By examining these examples, warehouse managers can learn how different technological tools can be tailored to specific operational needs, resulting in improved efficiency and productivity.
Implementing these technologies requires an understanding of both the potential benefits and the associated challenges. Success stories provide valuable insights and encourage other warehouses to adopt similar innovative strategies.
Inventory Optimization and Control Strategies
Effective inventory optimization and control strategies can greatly enhance warehouse efficiency and reduce costs. By focusing on key concepts like reorder points, ABC analysis, and efficient stock control, warehouse managers can minimize waste and improve overall operations.
Reorder Points and Inventory Turnover
Reorder points are crucial in maintaining a balanced inventory. Determining precise reorder points helps ensure that new stock arrives before existing supplies run out. This minimizes the risk of stockouts. Using inventory turnover ratios aids in understanding how quickly products sell. High inventory turnover indicates efficient stock management, while low turnover can signal overstock or slow-moving items.
To calculate a reorder point, managers should consider lead time and average daily use. Implementing a Warehouse Management System (WMS) can automate these calculations, providing timely alerts when stock reaches reorder levels. With accurate reorder points, warehouses can maintain optimal stock levels, reducing both excess inventory and the danger of running out.
Maximizing Inventory Accuracy with ABC Analysis
ABC analysis is a method used to categorize inventory based on value. Items are divided into three categories: A (high value), B (moderate value), and C (low value). This helps managers prioritize resources and focus more attention on items that contribute most to the warehouse's value.
For instance, Category A items require frequent monitoring due to their high importance. Regular cycle counts for these items help keep inventory records accurate. ABC analysis assists in setting different policies for each category, optimizing stock levels and distribution efforts. By focusing efforts on high-value items, warehouses can improve overall inventory accuracy and ensure critical stock is managed meticulously.
Reducing Operational Costs through Efficient Stock Control
Efficient stock control is essential for reducing operational costs. Implementing effective inventory control systems can prevent overstocking and stockouts, optimizing supply chain management. Techniques like Just-in-Time (JIT) inventory can greatly reduce holding costs by receiving goods only when they are needed for production.
Utilizing technology, such as barcode scanning and RFID, enhances inventory accuracy and minimizes errors. Efficient stock control limits the need for large safety stocks, freeing up capital and reducing storage expenses. This approach streamlines operations and ultimately leads to cost savings, making the warehouse more competitive in the market.
Effective Supply Chain and Logistics Management
Effective supply chain and logistics management involve coordinating various processes like warehousing, transportation, and procurement to enhance efficiency and customer satisfaction. This section highlights some strategies to optimize these operations within warehouse environments and beyond.
Optimizing Supply Chain Operations for Warehousing
A key element of supply chain operations is the efficient organization of warehouse activities. Streamlining inventory processes helps reduce waste and improve resource utilization. Techniques like Just-in-Time (JIT) and ABC analysis keep stock levels optimized. A focus on clear communication among warehouse teams ensures quick adjustments to changes in demand or supply.
Using technology can further enhance warehousing operations. Implementing Warehouse Management Systems (WMS) allows real-time inventory tracking, boosting accuracy. Automation, such as robotics and advanced scanning technology, can reduce human error and speed up processing times. These measures not only increase productivity but also lead to cost savings.
Integrating Transportation and Procurement Processes
Integrating transportation with procurement is essential for smooth supply chain management. Effective transportation strategies can involve choosing the right mix of transport modes, such as road, rail, or air, to balance cost and speed. Integrating logistics management with procurement ensures that goods are ordered and delivered on schedule, reducing delays.
Improving visibility across the supply chain can facilitate better planning and decision-making. Real-time tracking technology helps monitor shipments and track progress, providing data for future reference. By aligning procurement with transportation, businesses can achieve better negotiating terms with suppliers and carriers, ultimately enhancing efficiency and reducing costs.
The Role of Logistics in Customer Satisfaction
Logistics plays a crucial role in achieving high customer satisfaction levels. Timely and accurate deliveries build trust and dependability with customers. Efficient logistics management helps minimize delays and ensures that the correct products reach customers in optimal condition. Tracking shipments enables clear communication about delivery schedules.
Customer feedback can be a valuable tool for improving logistics operations. Regularly collecting and analyzing feedback helps identify areas for improvement, allowing businesses to make informed changes. By prioritizing customer needs through well-executed logistics strategies, companies can strengthen relationships and ultimately boost customer loyalty.
Key Performance Metrics and Continuous Improvement
Key performance metrics are essential for understanding and improving warehouse operations. By focusing on these metrics, managers can enhance efficiency and ensure a smooth workflow. Continuous improvement strategies are crucial for adapting to changes and maintaining a competitive edge.
Establishing Key Performance Indicators (KPIs)
Setting up effective KPIs helps warehouse managers evaluate critical aspects of their operations. These KPIs might include inventory accuracy, order fulfillment rates, and picking accuracy. Inventory accuracy, for example, ensures that stock levels match the records, reducing discrepancies and improving reliability.
Order fulfillment rates measure how efficiently orders are processed and delivered. High fulfillment rates lead to satisfied customers and repeat business. Managers can also track picking accuracy to evaluate the precision of order selections. Accurate picking minimizes errors, which in turn reduces return rates and enhances customer satisfaction.
Strategies for Continuous Improvement in Warehouse Management
Continuous improvement requires ongoing evaluation and adaptation of processes. Managers should regularly review KPIs and identify areas for enhancement. Implementing automation can streamline operations, reduce labor costs, and improve accuracy. Warehouse managers should embrace team collaboration to foster a culture of improvement and innovation.
One strategy is to conduct regular training sessions. This keeps staff updated on the latest procedures and technology. Encouraging feedback from employees on the floor can also provide valuable insights into potential improvements. By prioritizing these strategies, warehouses can remain flexible and efficient in a dynamic environment.
Measuring and Enhancing Warehouse Performance
To enhance warehouse performance, it’s crucial to measure performance metrics consistently. Key metrics include cycle time, order lead time, and space utilization. Shorter cycle times indicate a more efficient operation and quicker turnaround for customers.
Order lead time helps measure the time taken from receiving an order to delivery. Reducing lead times can be achieved by optimizing workflows and processes. Space utilization involves assessing how effectively the warehouse space is used. Efficient space management minimizes clutter, increases storage capacity, and improves accessibility.
By focusing on these metrics and implementing necessary changes, warehouse managers can boost operational performance and drive business success.
Warehouse Safety and Workforce Management
Effective management of safety protocols and workforce is crucial for maintaining a secure and efficient warehouse environment. Ensuring that safety measures are implemented and that the workforce is managed properly helps prevent accidents and boosts productivity.
Implementing and Monitoring Safety Protocols
Implementing safety protocols is essential for a warehouse. This involves identifying potential hazards and creating guidelines to prevent them. Regular training sessions for workers on these protocols can be beneficial. These trainings should cover areas such as forklift operation, manual lifting techniques, and emergency response procedures. It is also important to perform regular checks on equipment to ensure everything is functioning correctly.
Monitoring is just as vital as implementation. Regular audits and spot checks ensure compliance with safety standards. This can include checking for proper use of safety gear, like helmets and gloves, and ensuring clear pathways to avoid accidents. Feedback from workers about safety can provide insights into potential improvements.
Managing the Warehouse Workforce for Efficiency
To achieve efficiency in the warehouse, managers should focus on workforce management strategies. This includes scheduling shifts effectively to prevent burnout and maintain high energy and focus levels among employees. Utilizing technology, like warehouse management systems, can aid in tracking performance and output.
Clear communication is key. Regular meetings can help align goals and provide updates on productivity targets. Encouraging an open dialog allows workers to suggest improvements, boosting morale, and promoting efficiency. Setting clear expectations and providing the necessary resources ensures that the workforce performs optimally.
Building Authority and Visibility in Warehouse Management
Building authority and visibility are important in reinforcing roles and responsibilities within a warehouse. When managers establish themselves as knowledgeable leaders, it can inspire trust and reliability amongst the workforce. This starts with having a strong presence on the warehouse floor, actively engaging with employees, and showing a genuine interest in their work.
Creating a structured hierarchy ensures that roles are clearly defined. Regular feedback loops through performance assessments provide employees with an understanding of their progress and areas for improvement. Managers should also use technology to improve visibility, utilizing dashboards to monitor operations in real-time, which helps in making informed decisions quickly and effectively.
Building Communication and Training for Warehouse Teams
Improving communication skills in a warehouse setting can greatly enhance productivity. Training sessions reinforce these skills, ensuring everyone is on the same page. Utilizing editable templates can maintain consistency.
Crafting a Training Session for Warehouse Inventory Management
Creating a training session for warehouse inventory management requires clear objectives. Focus on processes such as receiving, storage, and shipping. Use PowerPoint presentations to make complex topics more understandable. Interactive elements like quizzes or role-playing are effective in engaging participants and reinforcing learning.
Incorporate real-life scenarios to connect theory with practice. Encourage questions to clarify doubts. Providing training materials and editable templates lets staff apply what they’ve learned in day-to-day operations, ensuring a practical understanding of inventory systems.
Effective Communication in Warehouse Operations
Communication in warehouse operations is crucial. Create a clear structure where each team member knows their roles and responsibilities and whom to contact with issues. Managers should use multiple communication methods, such as team meetings and digital platforms.
Active listening is vital. This involves understanding not just the words spoken but also the intent and emotions behind them. Encourage feedback to discover areas needing improvement. Using simple, clear terms can eliminate misunderstandings. Consider using multiple channels to ensure the message reaches everyone in a way they understand.
Editable Templates for Consistent Warehouse Communication
Editable templates can ensure communication uniformity across the warehouse. Create templates for inventory tracking, order forms, and daily logs, so everyone uses the same format. These templates should be easy to update and share, saving time and reducing errors.
Consistent templates help in maintaining records, streamlining processes, and providing clear reporting formats. Templates can be customized according to specific needs while maintaining a consistent framework. Regularly review and adjust templates to match evolving processes and technologies in the warehouse.
Enhancing Flexibility and Versatility in Warehousing
Flexibility and versatility are key in modern warehousing. Adapting to changes quickly can help in managing the flow of goods efficiently. Stockroom management should involve organizing inventory in a way that allows easy access and movement, which saves time and reduces errors.
A versatile warehouse can handle different types of products and order sizes. This requires adaptable order management systems that can process various order types without a hitch. Employing technology like barcode systems can simplify complex tasks, enhancing speed and accuracy.
Optimizing the order shipping process can also increase flexibility. Use a mix of shipping options to meet diverse customer needs. Adapting shipping methods based on order size or destination ensures timely delivery and keeps costs low.
Designing a flexible warehouse layout supports these goals. Adjustable shelving and open spaces make it easy to reconfigure the area when needed. Consider the use of modular systems that can scale up or down based on inventory levels.
Staff training is another vital aspect. Cross-training employees to perform multiple roles can increase day-to-day versatility. A workforce that understands various processes can shift their focus as demands change, reducing downtime and improving efficiency.
These strategies can contribute significantly to enhancing flexibility and versatility in warehousing, supporting smooth operations even in the face of changing business needs. For further tips on warehouse optimization, see this guide on warehouse optimization.
Frequently Asked Questions
Warehouse managers often face unique challenges in their roles. Understanding effective presentation skills, inventory management strategies, and leadership styles can greatly enhance their efficiency and effectiveness.
How can a warehouse manager improve their presentation skills?
A manager can enhance their skills by practicing clear and structured communication. Using visuals like charts and graphs can help make complex information more understandable. Engaging with the audience through questions and feedback is also beneficial.
What are key strategies for effective warehouse inventory management?
Effective inventory management can be achieved by utilizing warehouse management systems to track goods. Implementing clear labeling and categorization systems helps in locating items quickly. Regular audits and reviews ensure accuracy and efficiency in managing inventory.
What leadership styles are most effective in a warehouse management setting?
Transformational and servant leadership styles are often effective in warehouse settings. These styles involve motivating and supporting team members, as well as fostering an environment of collaboration. This approach encourages team growth and enhances productivity.
What steps should be taken to become an effective warehouse supervisor?
To become an effective supervisor, it's important to gain a thorough understanding of warehouse operations. Developing strong communication and problem-solving skills is crucial. Supervisors should also focus on training and mentoring team members to improve overall performance.
What are the best practices for managing a warehouse effectively?
Best practices include maintaining a clean and organized workspace, optimizing the layout for efficiency, and utilizing technology for tracking and reporting. Regular maintenance and safety checks ensure that operations run smoothly and that the work environment remains safe.
How does one provide effective training for warehouse management teams?
Effective training involves a combination of hands-on learning and classroom instruction. It is essential to cover both safety protocols and operational procedures. Continual learning opportunities and feedback help keep the team updated and engaged with the latest practices.